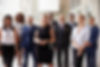
ISO Standards Certification Stages Using the PDCA Methodology.
As a ParagonQMS client, achieving ISO standards certification is an achievable and structured process.
By applying the PDCA (Plan-Do-Check-Act) methodology, the certification process becomes streamlined, focusing on continuous improvement and sustained success.
Below, we break down the certification process into clear stages and demonstrate how PDCA is embedded at each step.

01
Preparation and Planning (PLAN)
This is the foundation of the certification process. It involves defining your goals, understanding ISO requirements, and preparing your organisation for implementation.
Key Activities:
•Gap Analysis: Assess your current processes and compare them to the ISO standard. Identify areas that need development or adjustment.
•Define Objectives: Clarify why your organisation is seeking certification and outline intended outcomes
(e.g., improved customer satisfaction, operational efficiency).
•Project Planning: Develop an implementation plan, including timelines, resources, and responsible personnel.
•Training: Educate your teams on the ISO standard and their roles in implementing the quality management system (QMS).
Objective: To create a clear roadmap for achieving ISO certification, aligning organisational goals with the requirements of the standard.
Outcome:A well-prepared organization with a focused implementation strategy
02
Implementation (DO)

This stage focuses on executing the plan by developing or refining processes to meet the ISO standard. It’s about embedding the QMS into daily operations.
Key Activities:
•Document Development: Create required documentation, such as policies, procedures, work instructions, and manuals. It’s important that these documents are practical and align with real operations.
•Process Implementation: Roll out new or improved processes across the organisation . For example, introduce systems for risk management, customer feedback, or continual monitoring.
•Employee Engagement: Ensure all staff understand and apply the processes. Regular training and communication are essential here.
Objective:
To integrate ISO-compliant practices into daily business operations, ensuring these changes are effectively adopted by employees.
Outcome:
A fully implemented QMS that reflects the requirements of the ISO standard and is actively functioning.

03
Internal Checks and Audits (CHECK)
This is where the effectiveness of your QMS is evaluated to ensure compliance and identify areas for improvement.
Key Activities:
​•Internal Audits: Conduct formal audits of your systems, processes, and documentation to verify conformity with the ISO standard.
• Performance Monitoring: Use KPIs (Key Performance Indicators) and metrics to assess how well the system is performing.
•Management Review: Leadership reviews audit and performance data to evaluate the system’s efficacy in meeting objectives.
•Identify Nonconformities: Recognise deviations or gaps that need corrective action.
Objective:
To assess compliance, measure QMS performance, and gather actionable insights for improvement.
Outcome:A clear understanding of the QMS’s strengths and areas requiring action, paving the way for the next stage.
04
Corrective Actions and Certification Audit (ACT)

This stage involves addressing identified nonconformities, refining the system, and preparing for the external certification audit.
Key Activities:
• Corrective Actions: Implement solutions to the nonconformities or process gaps identified during the internal checks.
•Continuous Improvement: Review system performance and refine processes to enhance overall effectiveness.
Certification Audit:
oStage 1 Audit (Documentation Review): The external auditor reviews your ISO documentation to confirm readiness for Stage 2.
oStage 2 Audit (Certification Audit): The auditor assesses the implementation of your QMS to determine conformity with the ISO standard.
Objective:To ensure the QMS can withstand external scrutiny and demonstrate compliance with ISO requirements.
Outcome: Once nonconformities are resolved, and the external auditor approves your system, your organisation receives ISO certification.
Post-Certification – Maintaining the System
ISO certification isn’t the end of the journey; it's the beginning of a continual improvement cycle. The PDCA methodology continues to guide your efforts post-certification to maintain compliance and improve over time.
Key Activities:
•Periodic Audits (PLAN & CHECK): Schedule and conduct regular internal and external audits.
•Ongoing Training (DO): Train team members on changes and updates to your processes.
•Act on Feedback (ACT): Use customer feedback, audit findings, and performance data to continually improve your system.
Importance of Continuous Improvement:
By keeping the PDCA cycle active, you ensure your QMS remains effective, relevant, and aligned with changing business needs and standards.
________________________________________